Unlocking the Potential of Rapid Injection Molding Prototyping
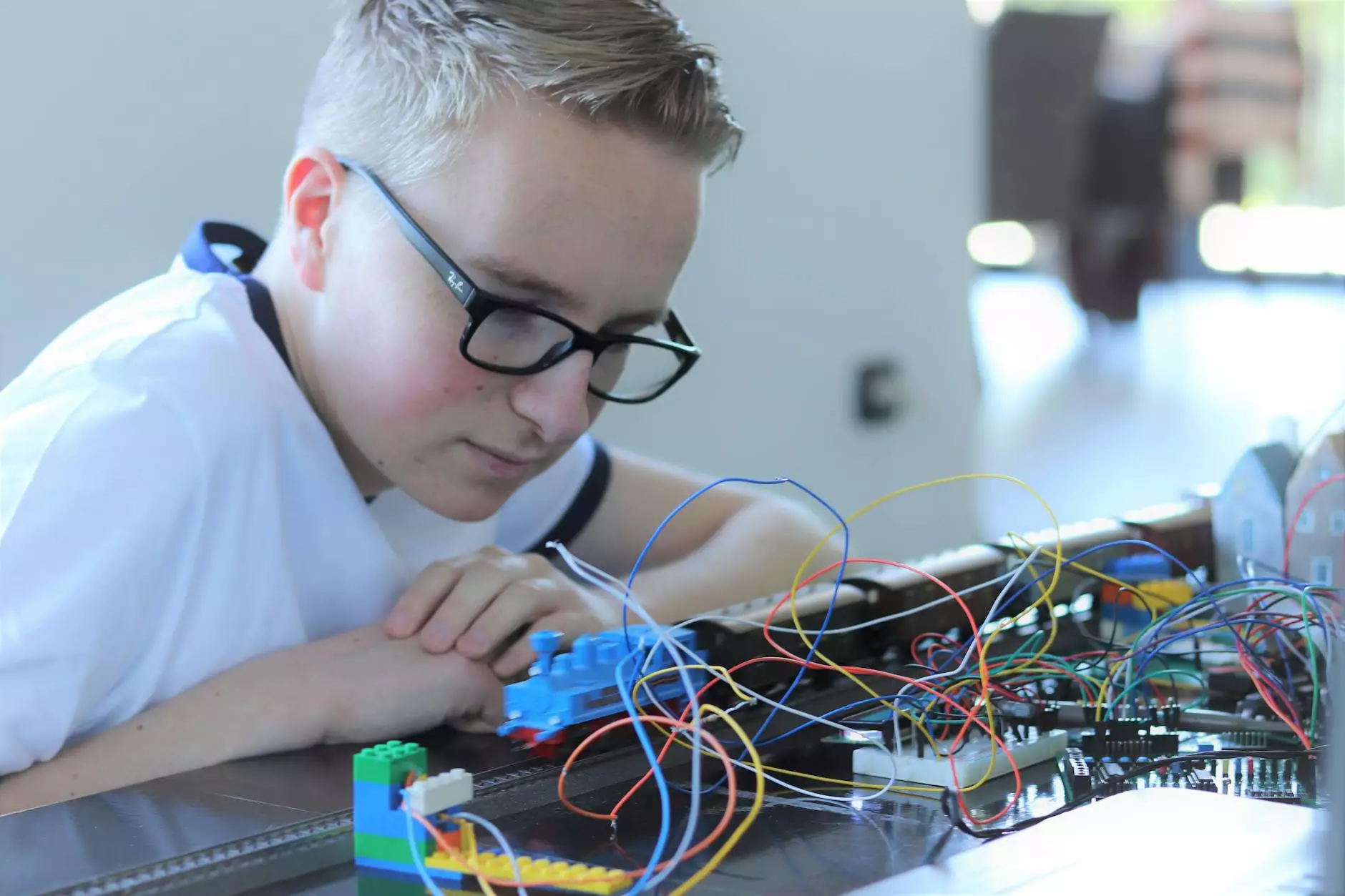
In today's fast-paced manufacturing landscape, businesses require agile, efficient, and innovative solutions. Rapid injection molding prototyping has emerged as a revolutionary technique in the metal fabrication industry, allowing companies to create high-quality prototypes much faster than traditional methods. This article explores the key features, advantages, and applications of rapid injection molding prototyping, reinforcing its value in manufacturing processes.
Understanding Rapid Injection Molding Prototyping
Rapid injection molding is a manufacturing process that quickly produces plastic parts using injection molding techniques. It is particularly effective for creating prototypes due to its ability to deliver high precision and fine details. The process involves several phases:
- Design Phase: Utilizing CAD software, engineers design a product that meets specific requirements.
- Tooling: A mold is rapidly created, often using high-strength aluminum, which is necessary for injecting the polymer material.
- Injection: Molten plastic is injected into the mold under high pressure, allowing intricate designs to form quickly.
- Cooling: The material cools and solidifies into the final shape, ready for inspection and use.
Benefits of Rapid Injection Molding Prototyping
The adoption of rapid injection molding prototyping offers numerous benefits to businesses in the metal fabrication industry:
1. Speed and Efficiency
One of the most significant advantages of rapid injection molding is its speed. The entire process, from design to finished prototype, can take as little as a few days. This rapid turnaround allows businesses to move from concept to production at an unprecedented pace, enabling quicker market entry.
2. Cost-Effective Production
Traditional prototyping can be expensive due to long lead times, extensive labor, and high material costs. Rapid injection molding reduces these costs through efficient design iterations and reduced material waste, which is crucial for startups and small manufacturers operating on tight budgets.
3. High Precision and Quality
Precision is vital in manufacturing, and rapid injection molding prototyping excels in producing parts with exact specifications. This technology ensures consistent quality across all prototypes, reducing the likelihood of defects and the need for extensive post-production adjustments.
4. Versatility in Material Use
Rapid injection molding supports a wide range of materials, including various thermoplastics. This versatility allows businesses to select materials that best match their product requirements, whether that be strength, flexibility, aesthetics, or chemical resistance.
5. Enhanced Design Validation
The ability to rapidly produce high-fidelity prototypes enables teams to validate designs effectively. They can conduct rigorous testing on real-world materials, ensuring that any potential issues are identified and resolved before moving to full-scale production. This iterative process mitigates risks and ensures a higher quality final product.
Key Considerations When Implementing Rapid Injection Molding Prototyping
While the advantages of rapid injection molding prototyping are compelling, businesses should consider several factors to maximize their investment:
1. Mold Design
The quality of the mold significantly influences the effectiveness of the rapid injection molding process. Engaging experts in mold design can lead to improvements in turnaround time and prototype quality. Utilizing simulation software can also help anticipate and resolve potential problems in mold design before production.
2. Material Selection
Choosing the right material is essential for achieving the desired characteristics of the prototype. Businesses should work closely with material suppliers to understand the advantages and limitations of various options. Testing different materials during the prototype phase can yield valuable insights for the final product.
3. Production Scale
Rapid injection molding is most beneficial for small to medium production volumes. If a product is expected to have large-scale production, moving to traditional injection molding methods might provide cost benefits as production volumes increase. It's essential to devise a comprehensive production strategy that considers future scaling possibilities.
Applications of Rapid Injection Molding Prototyping
The applications of rapid injection molding prototyping are vast and span numerous industries, including:
1. Automotive Industry
In the automotive sector, rapid injection molding is crucial for developing components, such as dashboards, housings, and fixtures. The need for lightweight, durable, and aesthetically pleasing components makes this technology invaluable in advancing automotive design and functionality.
2. Consumer Electronics
The fast-paced consumer electronics industry frequently requires prototypes to test and validate new designs. With rapid injection molding, companies can quickly develop prototypes for everything from enclosures to intricate internal components, significantly speeding up the product development lifecycle.
3. Medical Devices
Accelerated prototyping in the healthcare sector allows for the creation of intricate medical devices and surgical instruments. Precise and sterile designs can be produced quickly, enabling faster prototyping and testing which is critical for innovating medical technologies.
4. Aerospace Engineering
In aerospace, where performance and reliability are paramount, rapid injection molding provides an avenue for crafting prototypes that meet stringent safety and effectiveness criteria. The ability to test and iterate designs quickly can lead to significant advancements in aerospace technology.
Future of Rapid Injection Molding Prototyping
The future of rapid injection molding prototyping looks promising as technology continues to advance. Emerging trends such as the integration of artificial intelligence in design processes, advancements in material sciences, and automation of production systems promise to optimize the rapid prototyping process even further. As industries continue to seek efficient production techniques, rapid injection molding will undoubtedly remain at the forefront of the manufacturing revolution.
Conclusion
In conclusion, rapid injection molding prototyping stands as a game-changer in the metal fabrication industry. Its speed, cost-effectiveness, precision, versatility, and quality make it an indispensable tool for companies eager to stay competitive in a rapidly evolving market. By understanding and harnessing the benefits of this innovative process, businesses can not only improve their product development timelines but also ensure that they deliver high-quality products that meet market demands. As the landscape of manufacturing continues to evolve, those who embrace rapid injection molding technology will position themselves as leaders in their industries.
Explore the potentials of your next project with rapid injection molding prototyping at DeepMould.net. Your success is just a prototype away!